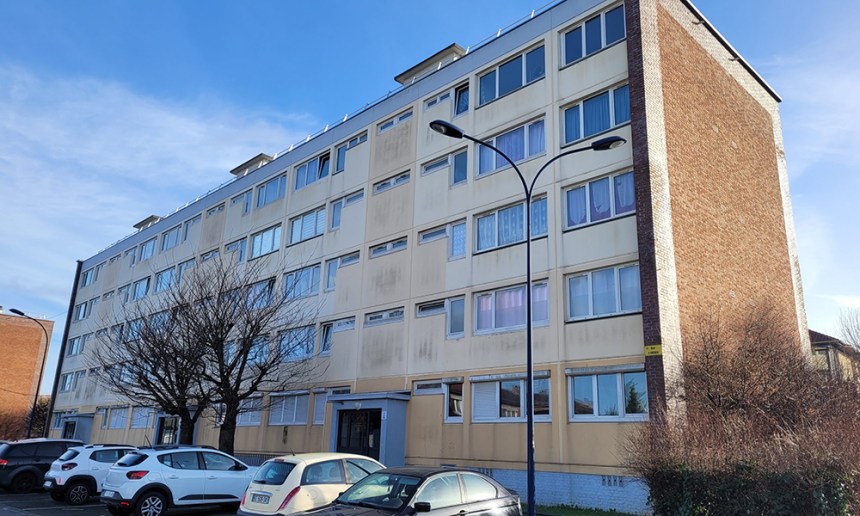
Fabrizio Leonforte, Associate Professor at Politecnico di Milano, explains how RE-SKIN is using circular renovations to improve energy efficiency in the built environment.
Our buildings need a serious upgrade to keep up with our changing planet. Winters are colder, summers are hotter, and outdated housing just can’t keep up.
The future of sustainable living demands smarter designs, cutting-edge materials, and game-changing technologies to make buildings more energy-efficient, comfortable, and resilient.
But what if the solution to this pressing problem lies not in the new, but in the sustainable renovation of existing buildings?
What is at stake?
With climate change driving increasingly extreme temperatures, energy poverty is becoming a year-round crisis.
In the EU, over 41 million citizens, 9.3% of the population, couldn’t keep their homes warm during the winter months and over double this (19%) were unable to cool their homes during heatwaves.
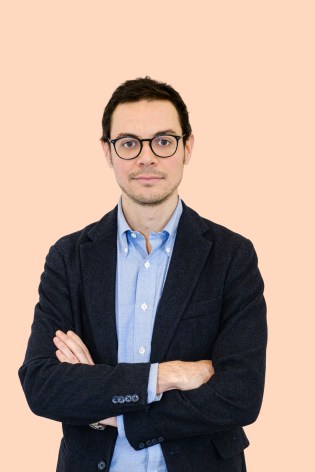
This is only set to worsen as our planet’s temperatures soar further. By 2100, up to 100 million Europeans will be exposed to extreme heat, a tenfold increase from today. Our cities and homes are simply not built to withstand this reality.
Moreover, it should be taken into account that buildings account for a staggering 40% of energy consumption in the EU, with heating and cooling making up 80% of that figure.
Poor insulation and outdated heating systems place a heavy financial burden on households, alongside the rising cost of energy.
At the same time, the building sector is responsible for 35% of Europe’s energy-related emissions. Without intervention, these numbers will only rise.
To align with the European Green Deal, these emissions must be reduced by at least 60% compared to 2015, within the next six years.
The key to reducing these energy-related emissions is investing in sustainable renovation that makes buildings more energy-efficient.
How RE-SKIN is driving circular renovation
One EU-funded project paving the way is RE-SKIN. From public housing in France and Spain to a Bulgarian school and a community-focused building in Italy, this project takes a holistic approach to renovation that integrates circularity with energy efficiency, fundamentally improving the lives of residents while cutting carbon emissions.
It is more than a technical upgrade; it is a social revolution aimed at making housing both affordable and sustainable.
The secret lies in renovating rather than rebuilding – using what we already have rather than starting from scratch – as it’s important to keep materials in use for as long as possible to reduce their impact on the planet.
RE-SKIN aims to cut energy consumption in existing buildings by up to 90% through an innovative, multifunctional retrofit system.
By integrating bio-based insulation materials, renovations can be carried out externally, allowing tenants to remain in their homes while improvements are made, making the process both efficient and socially inclusive.
Furthermore, the use of recyclable and dry construction materials cuts carbon output by 60% during the retrofitting phase and by 40% at the end of a building’s lifecycle.
The system is fully compatible with existing buildings without overloading structures and interfaces with the original installations.
It allows for low intrusive installation works, which decreases installation times and speeds up the overall renovation processes whilst reducing or avoiding discomfort for the inhabitants.
Inside a RE-SKIN renovation
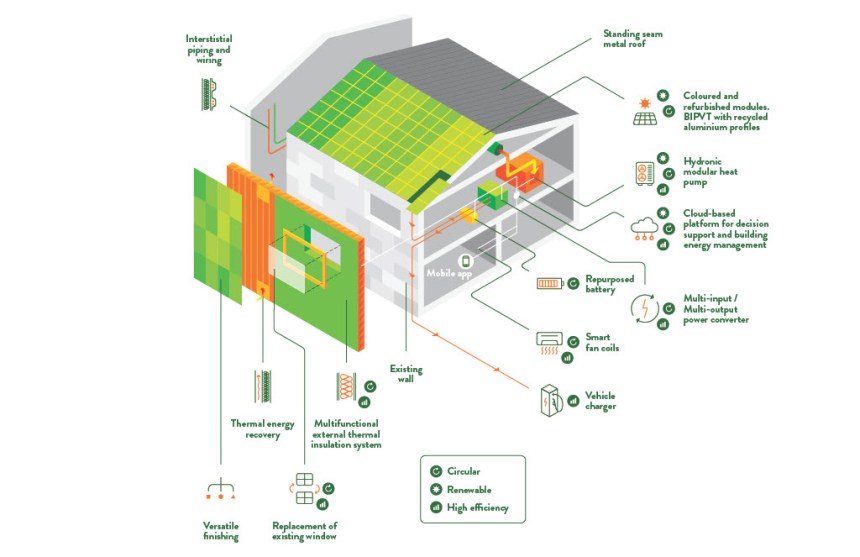
Instead of simply replacing old windows with new ones, RE-SKIN is taking a smarter, circular approach.
Existing windows will be upgraded with advanced coatings able to reduce the energy losses and to avoid the overheating – increasing the performances while saving labour and material cost.
By using recycled and bio-based materials, it is possible to cut energy consumption by 70% over the product’s lifecycle in comparison to standard materials.
Roofing is another crucial element of the retrofit process. RE-SKIN’s innovative building-integrated photovoltaic thermal (BIPVT) system builds on previous research to create roofs that not only withstand extreme weather but also generate electric and thermal energy.
By adapting curtain wall technology for rooftops, this system ensures better durability against heavy rain and strong winds.
Each roof is both resilient and environmentally responsible. The renovated buildings will have roofs made from recycled aluminium, bio-sourced insulation, and repurposed photovoltaic (PV) modules.
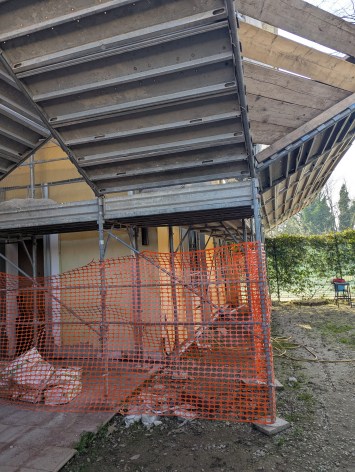
For areas not covered by solar panels, sustainable steel and bio-sourced insulation will be used, ensuring that every part of the building contributes to a lower carbon footprint.
The materials selected prioritise longevity, recyclability, and energy efficiency, proving that circularity can be seamlessly integrated into building upgrades.
Another key innovation is the use of repurposed electric vehicle (EV) batteries for energy storage. These discarded batteries, which are still functional and efficient, provide a cost-effective alternative to new storage systems.
By integrating batteries from the automotive sector, the solution reduces the environmental impact of battery production by up to 90%, significantly lowering costs over the system’s lifespan.
The evidence is clear. For a just transition, we cannot rely solely on the reduction of emissions in the operational phase, but we have to also consider the related embodied emissions throughout the whole life cycle.
Large-scale renovation projects prioritising circular materials and energy efficiency must become the norm.
The RE-SKIN project is proving that sustainable, affordable housing is not an unattainable dream but a practical, scalable solution.
The post How to tackle energy inefficiency through circular renovations appeared first on Circular Online.